Click, Clack, Clatter: Why is My PTO Making Noise?
Anyone who has been in the power take-off (PTO) business for long enough has run across a PTO that has made a noise that was somewhere between “kinda annoying” and “the truck sounds like it might shake apart.”
For every noise, there was likely a different word to describe it from everyone who has heard it.
Rattle.
Clatter.
Buzz.
Squeal.
Squawk.
Whine.
Clank.
Tick.
Click.
Clack.
The list goes on.
Although there are many descriptions for PTO noise, there are only a couple of noise categories that said descriptions fall into: Whine and rattle.
WHINE
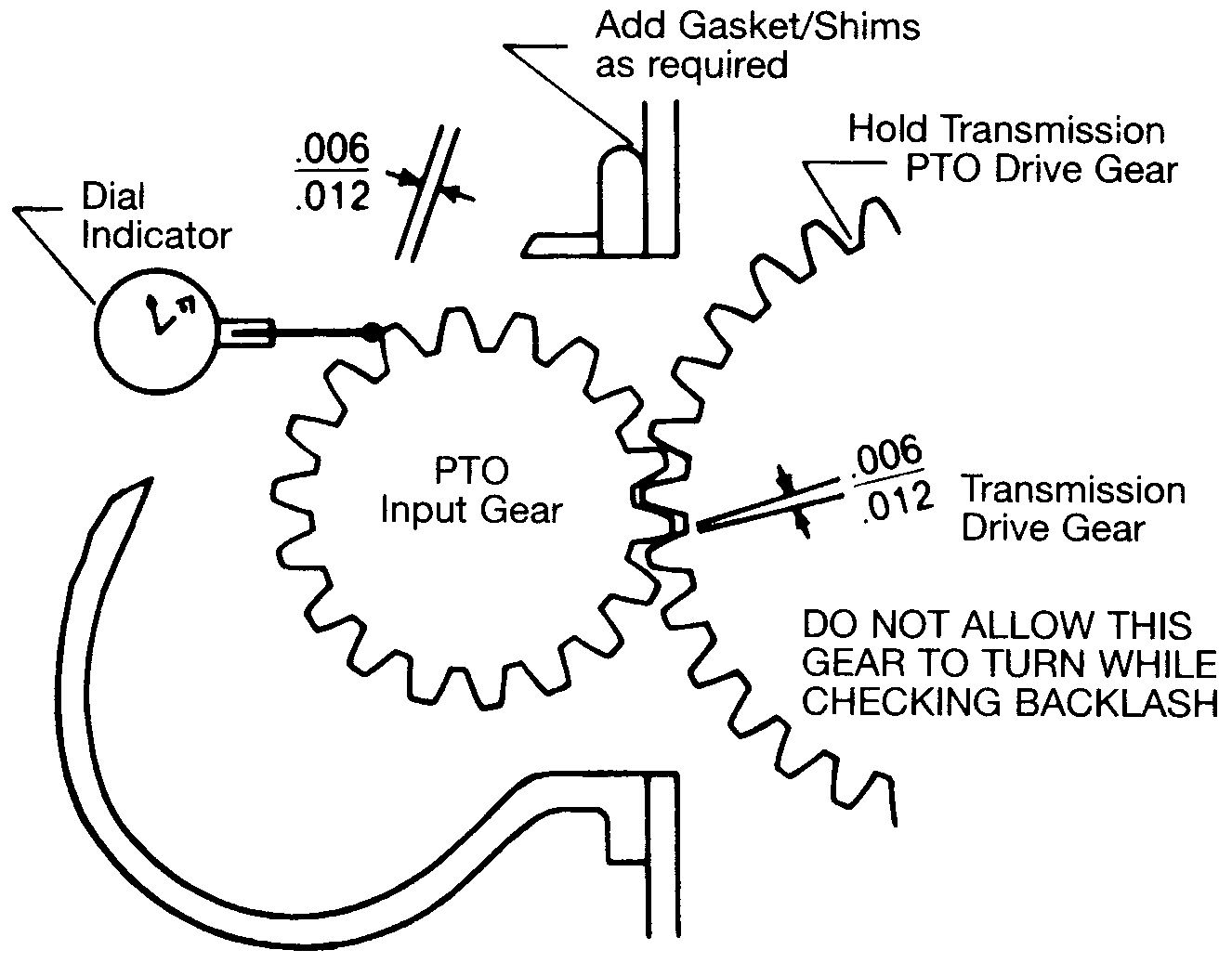
Above is a drawing of how to set backlash between the PTO and transmission. More on this process can be found by viewing the PTO Installation and Operator's Manual.
Most whining noises in a PTO come from either the gears or the bearings.
Gear whine is usually a high-pitched whine (or squeal) that occurs as a result of how the surfaces of the teeth on mating gears interact with one another as the gears rotate. Gear design and manufacturing quality play a large part in how much whine is present, but on most PTO installations exhibiting whining the cause is insufficient backlash between the input gear of the PTO and the gear in the transmission.
Adding additional shims between the PTO and the transmission will generally solve this problem as it provides the necessary clearance between the gears. The optimal backlash is between 0.006" and 0.012". It is important to note that a PTO with too tight of a mesh will have a much shorter service life than one with the correct backlash.
RATTLE
Rattle is a noise that most commonly occurs from two, unloaded, mating gears vibrating relative to one another. This is by far the most common noise complaint on PTOs. The noise emitted comes from the gear teeth on mating gears impacting one another as they rotate. On manual, automated manual, and automatic transmissions with a torque converter-driven PTO gear, this is typically a result of too much backlash between the PTO and input gear and transmission, as the gear teeth simply have too much room to move and bounce off each other. The solution for these applications is to reduce the overall shim thickness between the PTO and the transmission until the backlash is in the 0.006" and 0.012" range.
TORSIONAL VIBRATIONS
Some modern applications require more than just simple shimming to eliminate audible gear rattle. Automatic transmissions with an engine-driven PTO gear (often referred to as live drive) are the most difficult applications on which to reduce the audible output. This is due to the lack of any inherent damping of torsional vibrations created by the engine, which all carry through the gear train to the PTO.
For those unfamiliar with torsional vibrations, the vibrations are a result of the engine firing. When a cylinder is on the combustion stroke (fuel has detonated within the cylinder), the sudden acceleration of the piston down the cylinder is forceful enough to cause the crankshaft to flex. The crankshaft will then rebound. This flexing and rebounding is essentially what causes torsional vibration to take place.
As one might imagine, this makes for a tricky situation when it comes to eliminating gear rattle noise. On diesel engines, the amplitude of the vibrations is high enough that the PTO input gear teeth run into the back side of the ratio gear teeth, then bounce off, and hit against the front side. Without any form of gear rattle abatement, the resulting noise falls into the “the truck sounds like it might shake apart” category.
Fortunately, Muncie Power has developed a few different gear rattle abatement solutions to help mitigate the effects of torsional vibrations.
GEAR RATTLE ABATEMENT
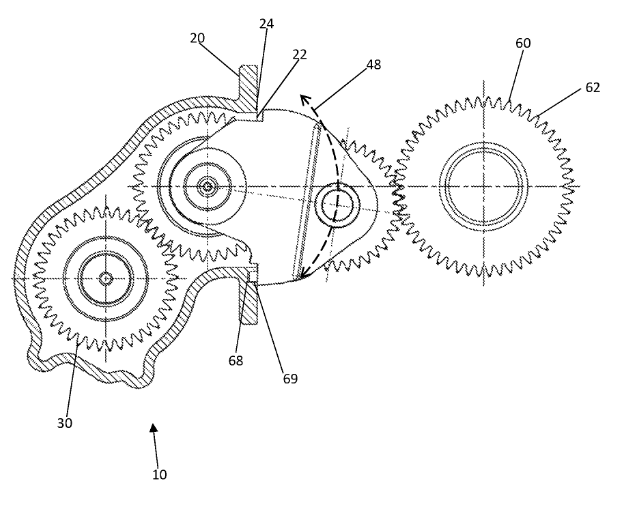
Above is a line drawing from the FR6Q Series patent for gear rattle abatement. The arrow, labeled 48, shows the path the rocker takes as it pivots around the idler shaft.
The first Muncie Power PTO series to incorporate a patented gear rattle abatement mechanism was the FR6Q Series. On this PTO, the input gear is held by a rocker that pivots around the idler shaft and is spring-loaded so that it presses the input gear into the transmission gear. As each vibration spike reaches the PTO, the input gear can bounce away from the transmission gear, with the energy being absorbed by the springs, rather than the back side of the gear teeth of the idler gear.
The second Muncie Power PTO series with patented gear rattle abatement was the F20 Series. This concept is like that used in the FR6Q Series, but without a pivoting rocker. The springs are positioned such that the PTO input gear can bounce up and down as the vibrations occur. It works similarly to shock absorbers on a car suspension. This same technology is also used on the F22 Series.
Other possible sources of noise to be mindful of are damaged gear teeth in either PTO or transmission and the PTO or mounted equipment being in contact with the floorboard, frame rail, or frame-mounted components. Drivelines that are out of phase or otherwise installed improperly can cause severe vibrations that may sound like they are coming from the PTO. Hydraulic noise might also be present, which is an article all unto itself.
This list is not comprehensive but does cover some of the most common causes of noise in PTO installations. If a PTO is exhibiting noise that seems beyond what may be considered typical PTO noise or is otherwise concerning, stop the truck and contact Muncie Power’s customer service team to discuss.