Direct vs. Remote Mounting a Hydraulic Pump to a Power Take-off
Featured Cover Story in Muncie Power Quarterly, Issue 3, 2017
Powering a hydraulic pump to a power take-off (PTO) is a common practice. Within mobile hydraulic applications, there are three types of hydraulic pump construction typically found including gear, piston, and vane.
Gear pumps are the most common design used in truck-mounted hydraulic systems, as the gear pump is relatively inexpensive with its fewer moving parts, ability to be easily serviced, and greater tolerance to contamination than other designs.
A hydraulic pump for mobile applications, like the gear, piston, or vane pump, can be either direct mounted to the PTO or remote mounted—using a driveline. While each type is a viable option for mounting a hydraulic pump, it is important to understand each type of mount to ensure an effective connection is made between the PTO and pump.
DIRECT MOUNTING A HYDRAULIC PUMP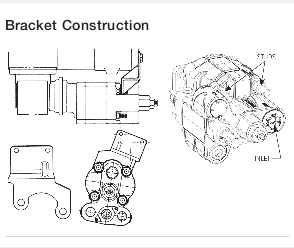
In a direct mount the hydraulic pump is mounted directly to the output flange of the PTO. Direct mounting is the most common type of installation in the mobile equipment industry. When direct mounting a pump, it is necessary to
- Specify a PTO output shaft and mounting flange that match those of the pump;
- Select the correct pump rotation to match the PTO output rotation or select what is known as a bi-rotational pump, which tends to have equally sized ports since either can be the inlet or outlet; and
- Provide a rear pump bracket to support the weight of the pump.
Anytime the combined weight of the pump, hose, and fittings exceeds 25 lbs., and/or the length of the pump is greater than 12 inches, it is necessary to provide a bracket at the back of the pump to support the weight. It is important that this bracket mount to two points on the pump and two points on the transmission case. Failure to install a properly designed support bracket will result in damage to the PTO housing and possible transmission failure when lubricant is lost.
RELATED: Pump Support Bracket Implementation and Design
Another concern to be wary of when direct mounting a hydraulic pump is a condition known as shaft fretting. This is rapid spline wear of the PTO and hydraulic pump shafts. The wear is evident at the place in which the two metal surfaces come into contact with each other, as the micro-movement of the two surfaces against one another wears each surface. This type of failure has increased with the advent of electronically controlled, diesel engines where conditions like harmonic vibrations originate in the engine, causing fretting corrosion that can lead to failure.
For mobile, truck-mounted hydraulic systems the most common pump mount is the SAE B, which is a 7/8" diameter shaft with 13 splines—one of the standard pump mounting configurations established by the Society of Automotive Engineers (SAE).
Advantages to direct mounting a pump
- Quicker, easier, and more cost-effective installations
- Less parts to repair and/or maintain
- No physical exposure to rotating components
Disadvantages to direct mounting a pump
- Concealed maintenance points, which include periodic removal and replacement of grease at the pump to PTO connection
- Space limitations
- Fretting or spline wear of the pump and PTO shafts
REMOTE MOUNTING A HYDRAULIC PUMP
Sometimes it is not possible to direct mount a hydraulic pump, requiring the pump to be remote mounted some distance away from the PTO and then powered from the PTO by means of a driveline assembly. The correct type and series of driveline must be selected. Solid shafting is not recommended as it cannot be balanced and can vibrate, damaging the PTO and pump shaft seals—causing leaks. The better choice is a balanced, tubular assembly designed to meet the speed, torque, and horsepower requirements of the application.
When using a driveline, it is important that it be in phase and incorporates a slip yoke at one end. Round, keyed PTO output shafts are susceptible to failure by high cyclic loading. An out of phase shaft will vibrate and damage the PTO and pump shaft seals while a functioning slip yoke will allow the shaft to adjust for flexing of the truck chassis. As part of a regularly scheduled, preventative maintenance plan, the slip yoke and bearings of the driveline must be lubricated.
As this type of installation has exposed rotating components it is important to make sure proper warning decals and guards are in place to protect workers.
Advantages to remote mounting a pump
- Space limitations are not a concern
- Exposed maintenance points make it easy to apply grease
Disadvantages to remote mounting a pump
- Additional cost to fabricate a driveline and remote mount a pump bracket
- Exposure to rotating components, which can result in injury up to and including death
Powering a pump to a PTO is a common practice, but selecting whether to direct or remote mount the pump takes understanding and careful consideration. Regardless of the type of mount you select, remember that this understanding of each mount—along with its advantages and its drawback—will be the key to creating an effective, lasting connection between the PTO and pump.